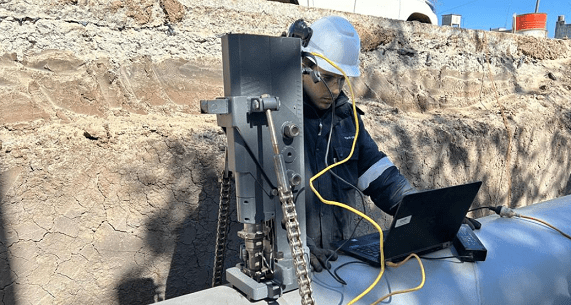
Instrumented Indentation: 15 years of experience providing know-how and technical support to the industry.
In 2008, we developed the instrumented indenter ESYS 10 with state support, allowing the industry to evaluate mechanical properties of materials without destructive testing. Over 15 years, only five companies worldwide offer this service, with GIE GROUP standing out in Argentina and Latin America. Learn more about its features in the following article.
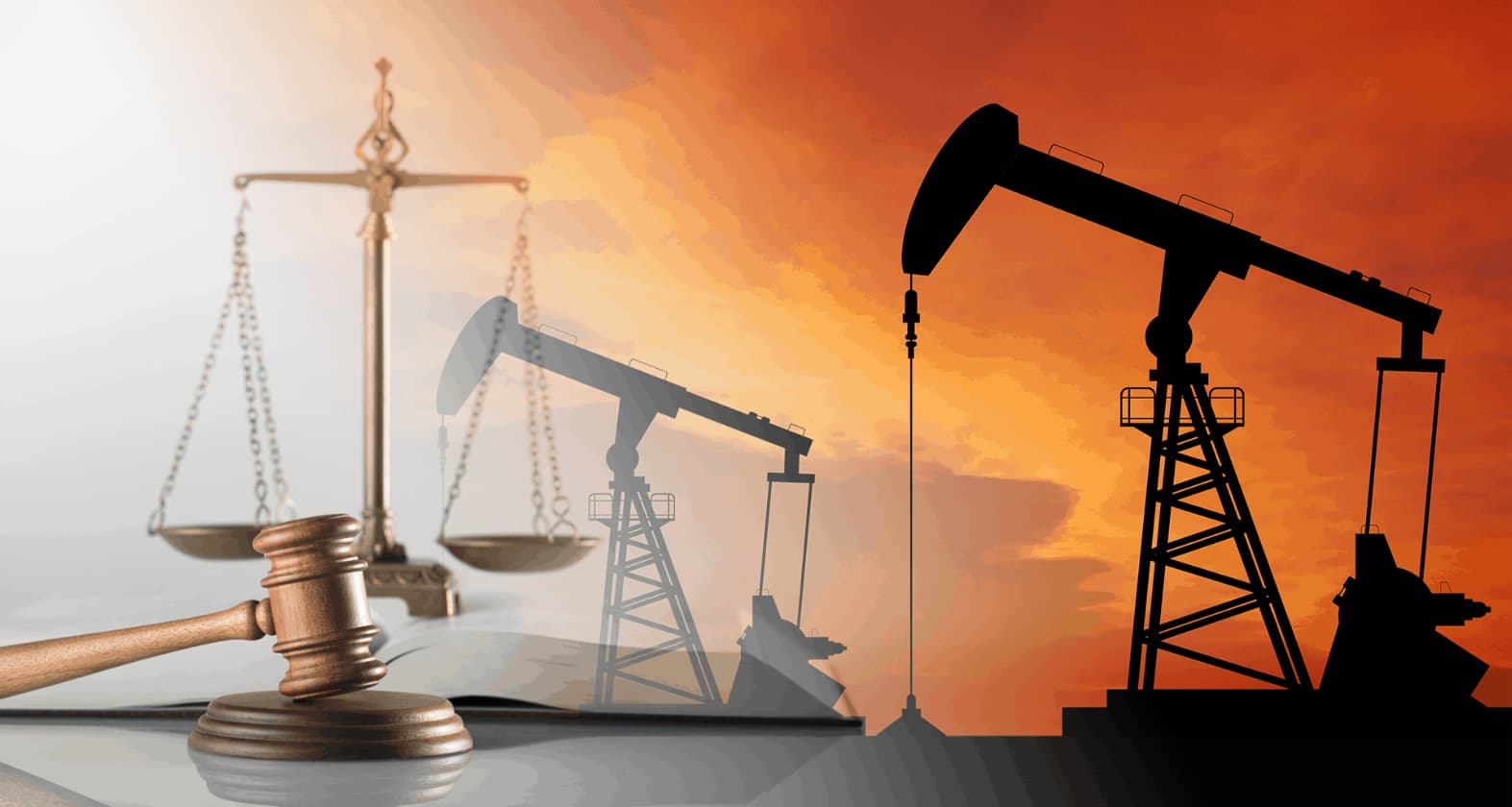
Protecting Assets and the Environment: Board of Directors Resolution No. 088-2022 - Risk Assessment in the Oil and Gas Industry in Peru
The Board of Directors Resolution No. 088-2022 from the Ministry of Energy and Mines (MINEM) in Peru establishes guidelines for the Security Risk Study (SRS) in hydrocarbon facilities. The SRS, crucial for ensuring safety in the oil and gas industry, encompasses hazard identification, risk assessment, and the establishment of preventive measures. The process includes the formation of specialized teams, a detailed description of facilities and processes, hazard identification using various methodologies, quantitative risk assessment, and the application of protection layers. Prevention and mitigation measures, along with periodic reevaluation, aim to maintain safe operations, reducing risks and minimizing environmental impacts, highlighting the importance of conducting the SRS not only as regulatory compliance but also as a tool for continuously improving safety and reliability in the industry.
Keep reading...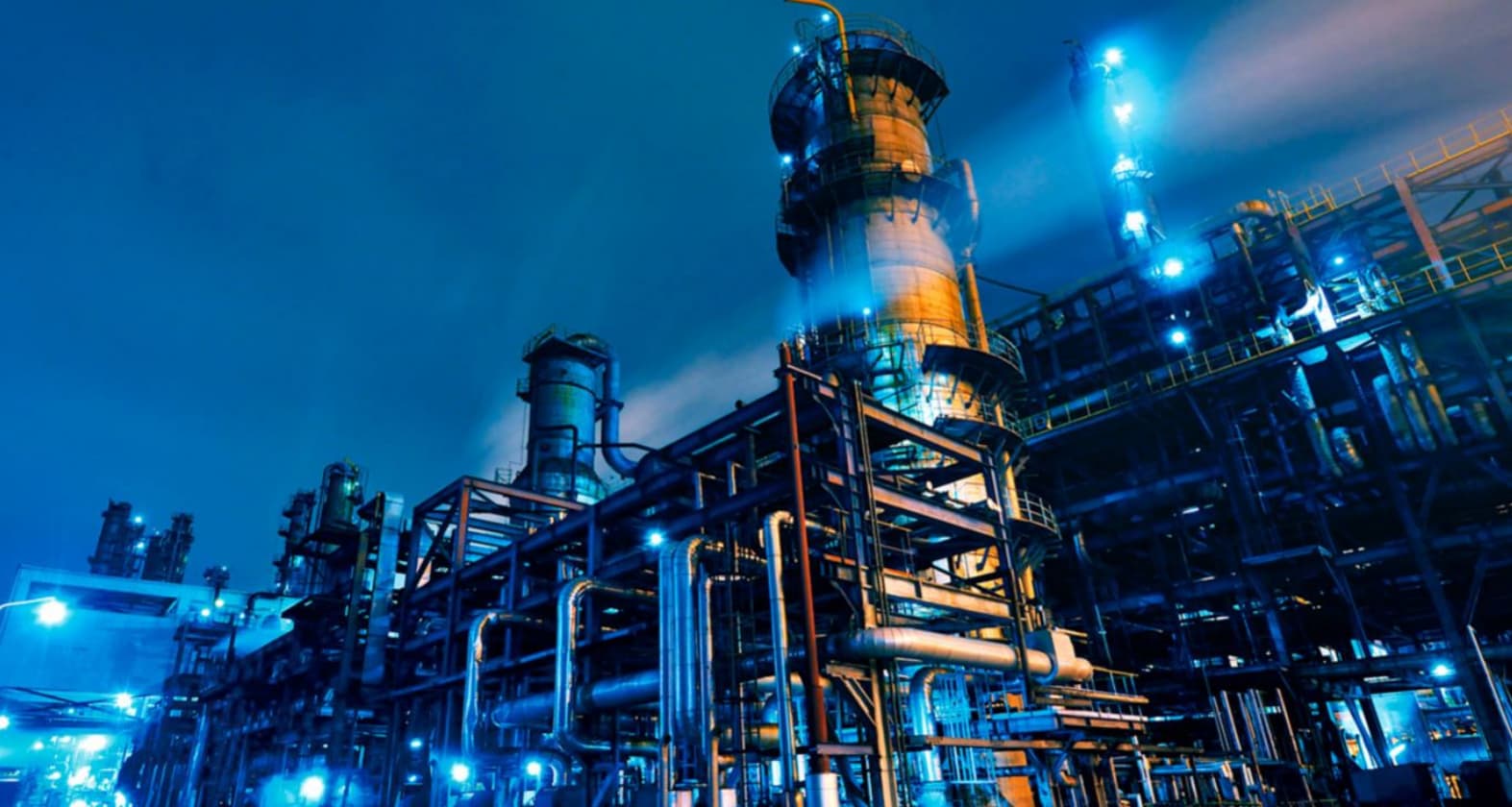
Exploring the Roots of Failures through RCA (Root Cause Analysis)
The Interest Note explores the concept of Root Cause Analysis (RCA) as a process to identify the fundamental cause of a failure in equipment, emphasizing that a failure implies the inability of the equipment to fulfill its original purpose. It is underscored that the consequences of these failures can be significant, affecting assets, people, or the environment. The scope of RCA has expanded beyond physical issues, encompassing areas such as corporate culture, quality management, occupational safety, project management, and medicine. The complexity of RCA will be addressed, emphasizing the need to identify events and conditions leading to failures. The importance of understanding failure modes and involved factors is highlighted for implementing preventive and corrective measures.
Keep reading...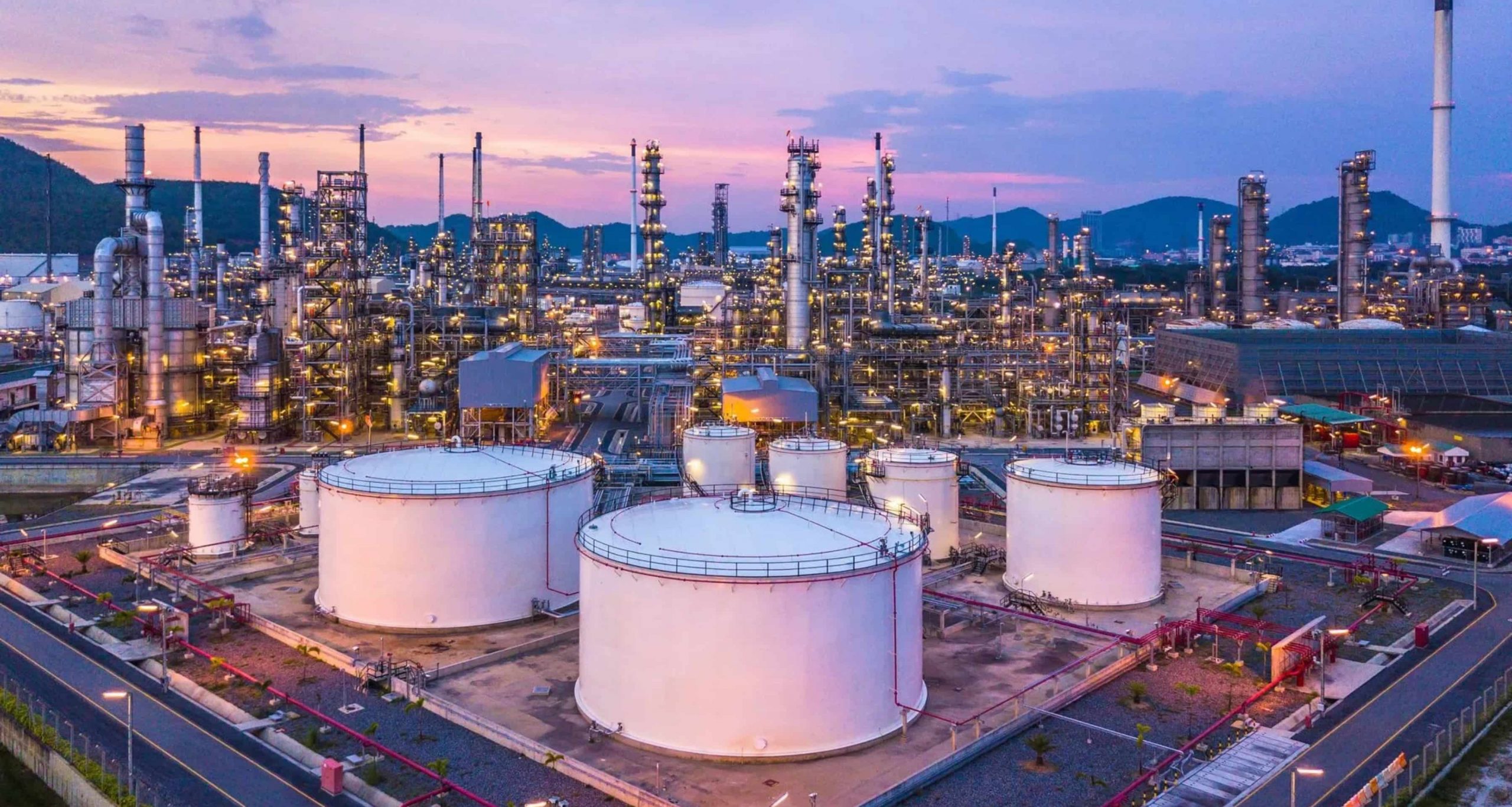
Implementation of Operational Integrity Windows
In the dynamic industrial environment, where assets face various threats that can compromise their integrity, the implementation of advanced methodologies becomes essential to ensure effective management and extend the lifespan of equipment. In this context, we emphasize the relevance of "Integrity Operating Windows" (IOW) as a fundamental component in the maintenance strategy. These operating windows not only provide a proactive approach for continuous monitoring of critical variables but also allow anticipation of potential deviations in asset performance. Through the definition of key variables, operational limits, and responses to these limits, Integrity Operating Windows emerge as a comprehensive tool for early detection of deterioration, facilitating informed decision-making and significantly contributing to reducing uncertainty in asset management. In this context, we will thoroughly explore the application and benefits of these operating windows in predictive maintenance and continuous improvement related to the integrity of industrial assets.
Keep reading...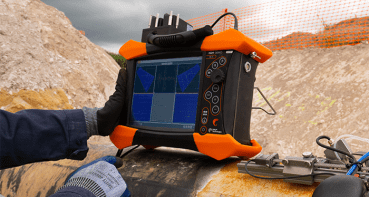
Discover the Advantages of Phased Array Ultrasonography (PAUT) for Weld Inspection and Corrosion Mapping
Phased Array Ultrasonography (PAUT) is an advanced method that utilizes multiple ultrasonic crystals with varying delays to generate directed ultrasonic beams at specific angles. Unlike conventional ultrasound, PAUT probes can be electronically focused without the need for physical movement, facilitating the inspection of seams and other critical areas. It can be applied manually or connected to equipment such as crawlers to record the position, similar to digital radiography.
PAUT offers significant advantages over conventional ultrasound, including increased certainty and speed in inspection. Sectorial and linear scans enable comprehensive coverage of welds and the detection of discontinuities. Furthermore, PAUT replaces industrial radiography in pipeline construction, producing permanent records without radiation, thereby enhancing safety and efficiency in inspection. The method is also effective for corrosion detection and determining corrosion profiles. Overall, PAUT is a versatile technology applicable in various industrial sectors.
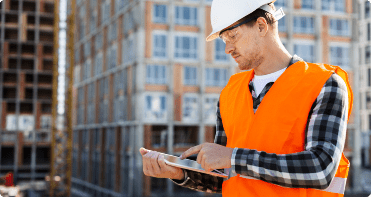
Real-Time Digital Survey
In the industry, the collection of information, data capture, and activity logging on paper have been a tedious and error-prone process. This working methodology has led to inefficiency in planning, task allocation, and results review, as well as the generation of a large number of unnecessary documents and errors. However, the availability of technology such as laptops, tablets, and smartphones has enabled a more efficient solution for data gathering.
Two application examples presented in this article illustrate how this technological solution has transformed the industry. In the first case, at a gas expansion plant, a solution was implemented using Lemon Forms to expedite visual inspections. In the second case, during the inspection of injection wells in oil fields, a customized form was developed, allowing for the rapid evaluation of well suitability and risk assessment.