In any industry, there are always necessary activities related to information gathering, data capture, operator or security patrol records. We know that paper-based surveys can be tedious, as they later need to be digitized and formatted, etc. This process is often cumbersome and ends up consuming a lot of post-processing hours to achieve the desired goal.
Conducting paper surveys has the following disadvantages:
- Efficiently planning and scheduling work
- Assigning work to inspectors already in the field
- Rework due to errors in data collection
- Time consumed in result review
- Fluctuating quality of reports depending on the inspector’s organization
- Manual tracking of key indicators and project progress
- Manual entry into Excel, Google Sheets, etc.
- Large amounts of paper and unnecessary copies
- Significantly increased error possibilities
With the availability of current technology such as notebooks, tablets, smartphones, etc., a much more efficient process can be achieved for information gathering. This is based on leveraging the technology of survey devices, as they can combine writing, diagram or schema creation, photo-taking, OCR, etc.
The first step in implementing this technology is to understand the survey’s objective and design the desired output format, with a clear understanding of the final report format and organization. It is possible to develop a survey form for organized data capture, including the necessary options that will later allow the use of aggregated information, concise statistics, or indicators for the situation to be surveyed.
In addition to improving data capture format, the task assignment and review process can be optimized, as the application includes a program that allows assigning personnel to perform the survey and personnel to review them (if necessary), with an approval scheme, traceability, and historical records of the steps taken.
Programming
• Assign Survey Personnel
• Assign Review Personnel
Execution
• Survey Execution
• Review and Approval of Survey
Delivery
Instant Record Availability
Post-processing
Compilation of Information to Create Specific Statistics or KPIs in MS Excel or Compatible Format
It is a solution that allows replacing old paper surveys with web and mobile applications designed to suit, accessible from PC, notebook, tablets, and smartphones with or without internet access.
Application Examples #1.
Turboexpander Plant Inspection in Latin America.
This involves a gas expansion plant with a capacity of 5 MMm3/d, which required a significant overhaul and revamping for new process conditions. The need arose to perform a complete integrity assessment of the plant, involving the following activities:
- Internal and External Visual Inspection
- Thickness Measurement (Scan B and Scan C)
- Magnetizable Particle Testing
- PMI Testing (Material Identification)
- Panoramic Radiography
- Others
One of the main challenges was to conduct the inspection in a very limited time frame. As part of the strategy to meet the scope in that tight timeframe, a solution was implemented using Lemon Forms for visual inspection activities. Specific forms were designed for this purpose, namely:
- Visual Inspection Form for Lines, based on API 570 and 574
- Visual Inspection Form for Vessels (Internal and External) based on API 510
- Visual Inspection Form for Heat Exchangers based on API 510 and 572
- Visual Inspection Form for Air Coolers based on API 510 and 572
- Visual Inspection Form for Tanks based on API 653
- Visual Inspection Form for Furnaces, according to API 572 and API 530
The implementation of Lemon Forms allowed our inspectors to substantially accelerate the visual inspection process, while maintaining the highest standards of international equipment inspection regulations. Some figures of the activities performed that we were able to record are:
[wpdatachart id=1]
[wpdatachart id=2]
A comparison was made between the time spent on field surveys and office reviews, with the times of projects previously executed without the Lemon Forms tool. The result involved a savings of about 660 working hours on average, a 36% reduction in time spent on these activities. Considering the prices of services, this benefit resulted in savings of approximately USD 25,000 for the client.
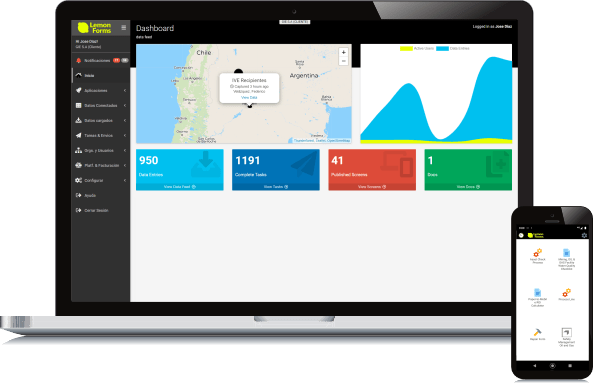
Lemon Forms: Real-Time Digital Survey Solution
Application Example #2
Injection Bridge Inspection
In mature production fields, it is common to use secondary recovery techniques. Secondary recovery basically involves injecting a fluid into the reservoir to maintain an acceptable pressure gradient. These fluids are injected through injection wells and displace or sweep some of the oil to production wells. It is crucial to maintain the operational reliability of these injection bridges, which have been in operation for several years, by conducting their inspection and subsequent integrity evaluation.
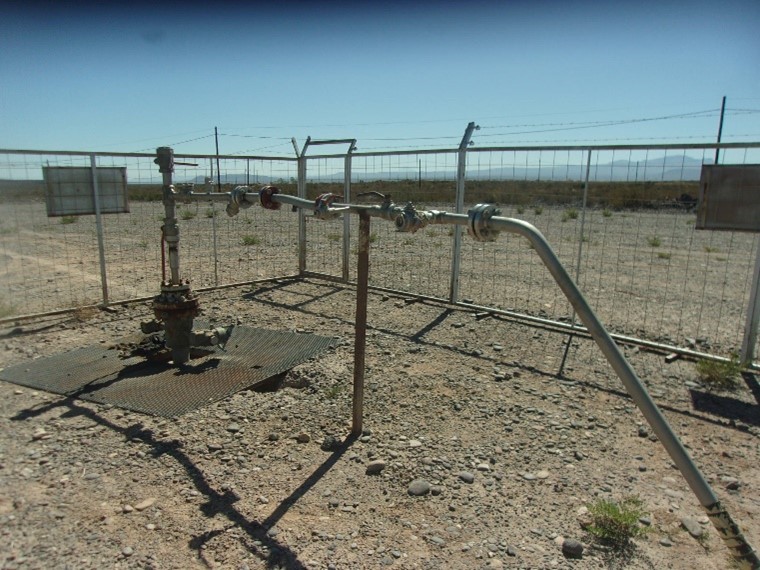
Injection Bridge Inspection
In recent years, GIE started inspecting to verify the fitness of injection wells, implementing techniques such as:
- Visual Inspection
- Thickness Measurement
- Panoramic Radiography
Injection bridges have configuration similarities depending on their location, making it possible to develop a customized inspection form for this type of asset in the Lemon Form application.
In collaboration with our client, an evaluation method was designed to quickly determine critical aspects of the bridges. Some of these aspects include:
- Presence of Carbon Steel Accessories
- Damage from external corrosion
- Status of the coating
- Verticality
- Support condition
- Instruments
- Presence of leaks
This method determined which of the conditions found determined the level of risk for each one or even whether it was necessary to take a certain well out of operation, as well as an emergency communication scheme when urgent interventions were required.
The developed form allowed the incorporation of a risk assessment algorithm, based on certain predefined variables, to quickly evaluate the configuration of each bridge and obtain a risk value for each one.
An inspection and evaluation campaign of 410 injection bridges was conducted, allowing the evaluation of the risk level and fitness for each one in just a few months. In addition, the Lemon Form application allows the compilation of similar recommendations grouped by urgency, adding value to the service by providing a practical summary for defining necessary urgent mitigation actions.
As for inspection times, there was a 20% reduction in field inspection times and up to a 60% reduction in office activities, avoiding the tedious work of organizing, presenting inspection photos, transcribing comments, and making specific recommendations, as they are predefined based on findings.
Conclusions
We have seen how the adoption of simple and low-cost digital technologies can significantly increase the reliability and quality of inspection services while generating significant time savings, often a critical variable for operators.
Additionally, the custom design of forms facilitates result interpretation and the planning of activities following the Integrity Evaluation.
GIE GROUP, through its LEMON FORMS solution, has been an early adopter of these technologies and has an experienced group of Integrity Engineers for the implementation of the process.