In any industry, assets face threats that can result in a reduction of their operational capacity, unplanned service interruptions, or the need for replacement before the end of their lifespan. In any case, the condition of these assets leads to a constant increase in uncertainty. This is where predictive maintenance activities allow us to narrow down the situation and generate sufficient information for effective decision-making, maintaining and even extending their lifespan.
Implementing inspection plans qualifies and/or quantifies the state of some key parameters to assess asset performance. If this activity is carried out generically, based on inspection standards and without an analysis of expected damage morphologies, the result may be biased, overlooking specific morphologies that deviate from the typical ones (such as pit-type corrosion, corrosion under insulation, or cracking mechanisms, for example).
Whether within the context of Risk-Based Inspection (RBI) methodologies or through the execution of a damage mechanisms study, having expected damage morphologies streamlines the approach to threats and their evaluation. However, their evaluation through non-destructive testing remains an activity with a certain periodicity, and in the meantime, uncertainty continues to increase.
The incorporation of integrity operating windows methodologies allows continuous monitoring of key variables for asset deterioration, whether due to the appearance or changes in the severity of mechanisms. It is based on defining variables, operating limits, and responses to these limits. Implementation requires multiple instances and significant interaction between maintenance, processes, instrumentation, and operations (among others).
Early detection of deviations in variables allows for actions to regulate or neutralize the variation, as well as identifying the effect on other variables and collateral effects of the actions taken. On one hand, it is possible to anticipate damage, minimizing its impact on the health of related assets, and on the other hand, it allows studying the behavior and generating models that assist in predicting the response of systems to changes induced by operation or stream composition.
Theoretical
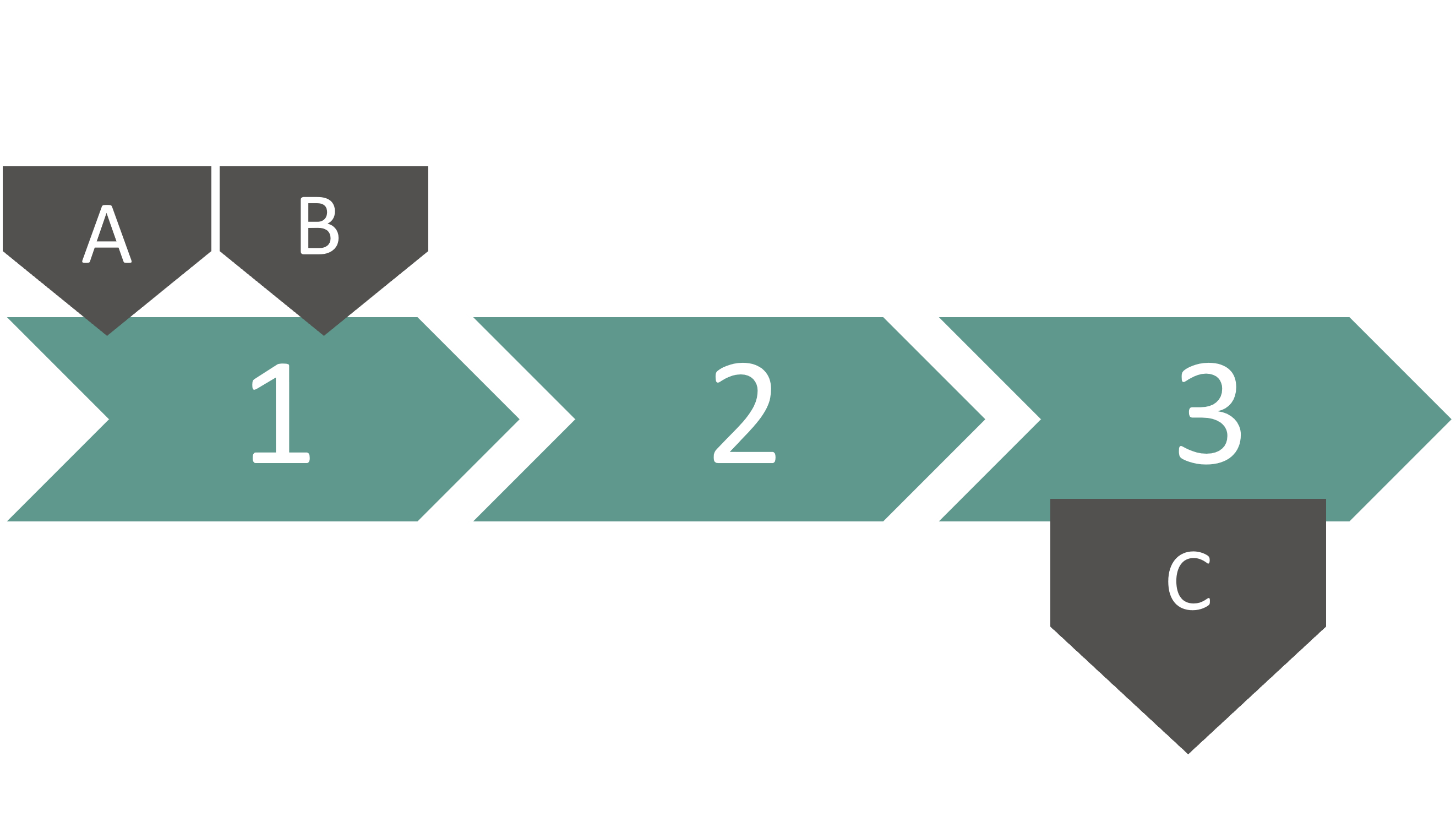
- Definition of Key Variables
- Determination of limits, sampling frequencies, and location
- Action plan for each case
- A. RBI
- B. Analysis of Damage Mechanisms
- C. Action Plan
Application
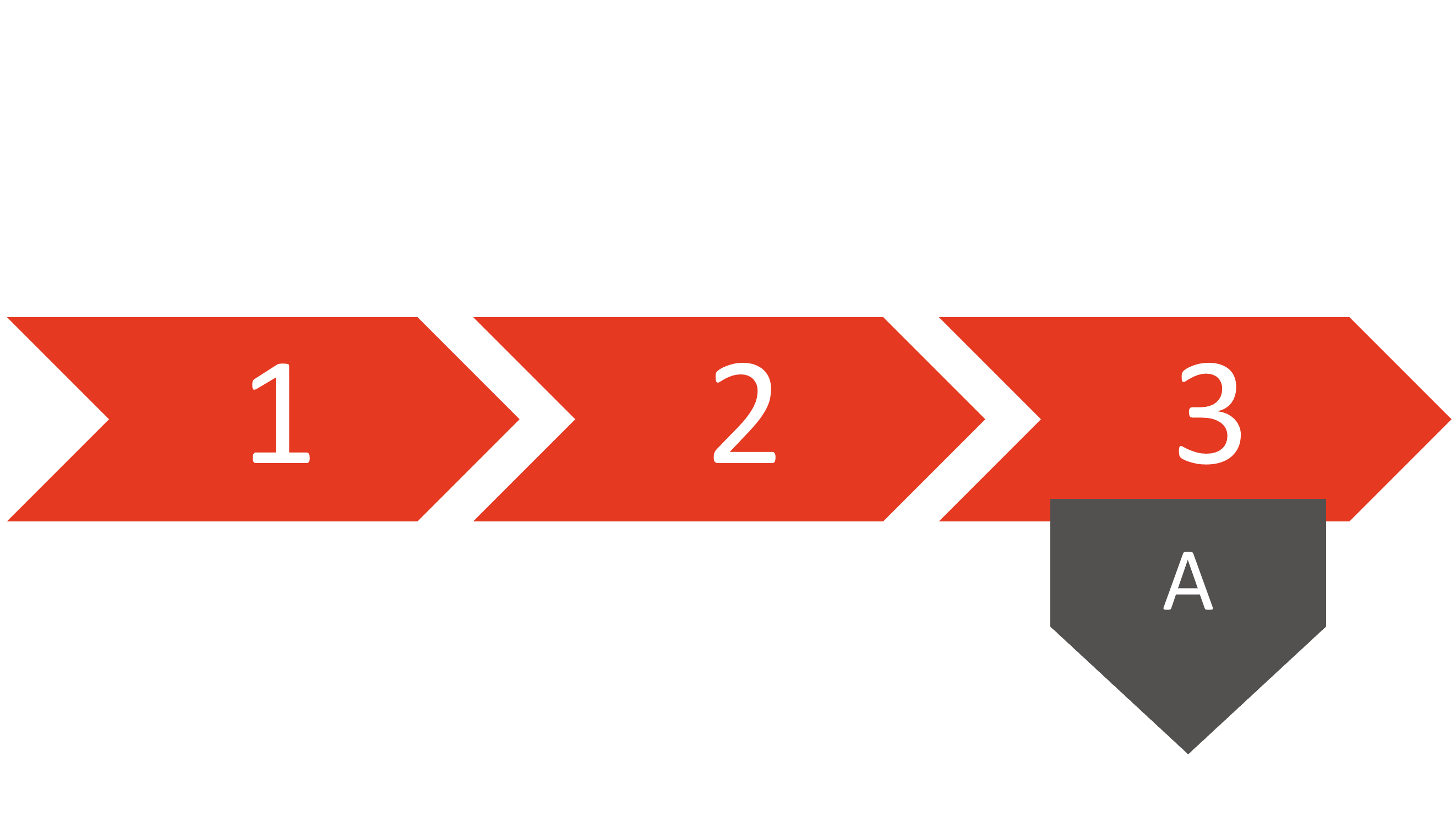
- Identification of Monitored and Missing Variables
- Budgeting for Gap Adjustments
- Incorporation into monitoring systems
- A. Implemented Operating Windows
The implementation procedure of the methodology starts with an academic approach where the monitoring procedure for variables will be studied and defined. After this stage, the application phase begins, where data collection and control are materialized.
The first step is the analysis of active or potentially active damage mechanisms. At this point, it is crucial to distinguish between those mechanisms that have been qualified or quantified as active (indicating the presence of operational mitigating actions) and those that could theoretically occur. In this context, the concept of corrosion loops becomes important, allowing an expanded view of the experience to areas of the asset with similar conditions. In complex processes, it is possible to apply a criticality ranking of variables (and monitored mechanisms) to focus implementation efforts of the methodology.
Contact Our Specialists Today
We will assist you through the combination of the best professionals, highly trained and with extensive experience, and the use of the latest technology, all aligned with the best management practices
Click the following link to schedule a meeting
Contact Form
With identified damage mechanisms, the next step is to determine the key variables to monitor for each of them. At this stage, interaction with operations and processes is important to identify which variables are already monitored. Once the variables are defined, limits (alert and alarm), sampling frequencies, and data collection locations (for those not instrumented) are determined.
Next, response protocols are established for each defined deviation. Responses can vary from adjusting chemical injection, inspecting key points, controlling related variables, or simply notifying the deviation for record-keeping.
After completing the academic exercise, the most complex step begins, where support from other areas plays a crucial role in advancing the initiative. For variables that are not currently monitored, it is time to design the instrumentation and integrate it with monitoring systems (for continuous monitoring variables). Some variables can be taken through periodic sampling; in such cases, the challenge is to integrate new practices into the workflow so that the relevant personnel report the results of the sampling in a timely manner. Instrumentation generally represents the most significant investment as it involves installing equipment for monitoring and making changes to the work structure for the incorporation of the new activity.
While the
base study covers a large part of the academic exercise, with monitoring in progress, the investment in reviewing and evaluating results will continue with a significantly lower economic impact (reviewing trends and responses to changes). With a frequency determined on a case-by-case basis, a review of the definitions of the base study will also be proposed using the historical data from monitoring (either through a review of RBI – Risk-Based Inspection or a DMR – Damage Mechanism Review). From this evaluation, it will be possible to continue as is, adjust window parameters, or incorporate new variables.
The incorporation of such methodologies not only represents an improvement in the view of the asset’s situation but also fosters interaction between areas, providing visibility to actions taken on both sides. Another associated benefit is adding actions to prevent mechanisms from escalating in severity, achieving a reduction in uncertainty. For these reasons, the incorporation of IOW methodologies in processes represents a perfect complement to inspection and maintenance activities that ultimately allow better asset performance.