Introduction
Radiography is an inspection technique with a long history in the industry, primarily for weld inspection, which has remained virtually unchanged. In the early 2010s, digital radiography began to be used timidly. Over time, digital technology experienced significant evolution, greatly expanding its field of application and effectiveness. Being digital, this inspection method offers a series of benefits and new applications that must be evaluated and considered when defining how structural integrity evaluations and defect detection in various materials and industrial components are carried out.
Advantages of Digital Radiography
There are many reasons to migrate from traditional radiography inspection to digital radiography and additionally use it for solutions where it was previously not considered. This technology has several advantages over its predecessor:
Storing and sharing results: Digital radiography images are saved in digital format, greatly facilitating their distribution via email, storage on dedicated servers, and subsequent reevaluation quickly and easily over time.
Reducing radiation exposure time: Due to the harmful effects of radiation, one of the limitations of industrial radiography is the need to delineate work areas, which generates interference and delays with other tasks. Digital radiography allows for greater detection sensitivity, resulting in a significant reduction in radiation exposure during the inspection process. Additionally, it is possible to use X-rays instead of gamma rays, which reduces the fencing distance, thus not hindering other tasks and also reducing the risks of transporting the source.
Reduction of inspection and evaluation time: By eliminating the chemical development procedure, it significantly speeds up the process. Images can be viewed, depending on the Digital Radiography method, immediately on a tablet, laptop, PC, etc., or a scan that takes 1 minute must be performed.
Environmentally friendly: 100% of chemicals are eliminated, there is no need for final disposals, plates are eliminated, radiation exposure time is reduced as already mentioned, resulting in sufficient benefits to migrate to this type of inspection.
Better images and the possibility of better analysis of them: Being able to perform in-situ tests with X-rays, something unthinkable 20 years ago, these high-resolution digital images allow for more precise defect detection and detailed evaluation. There is specialized software that allows processing and enhancing them to highlight areas of interest, perform precise measurements, and carry out an initial defect analysis automatically.
Different Digital Radiography Technologies
It is important to know that energy generation, produced by X-rays or Gamma rays, is independent of the digital radiography detection technology. Either source can be used by traditional or digital methods, always considering that there are limitations depending on the thickness and inspection distance.
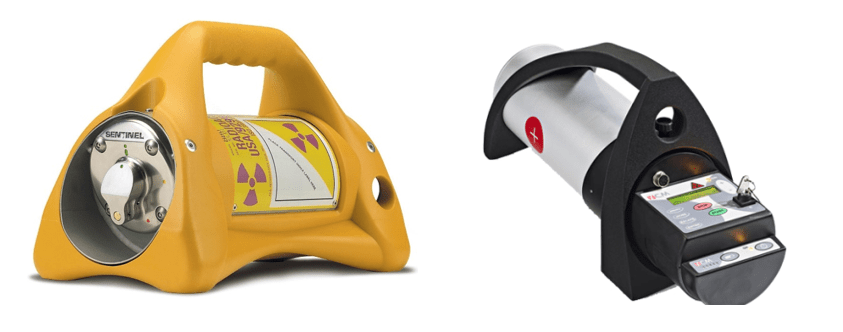
Image 1 Sentinel delta 880 gamma-ray equipment and portable X-ray generator with battery
There are two main digital radiography technologies, Flat Panel and Phosphor Plates. Among them, there are many differences, from portability, sensitivity, detection technology, and the exposure time needed. We will mention that the Flat Panel is rigid, the image is observed at the end of the test on a device such as a tablet or laptop. It has dimensions suitable for panoramic plates, for example, for corrosion search, and is not focused on seam examination. On the other hand, Phosphor Plates are flexible, development is done after the test through a process that involves scanning the plate, which is “erased” at the same time to be reused and is generally used for seam examination.
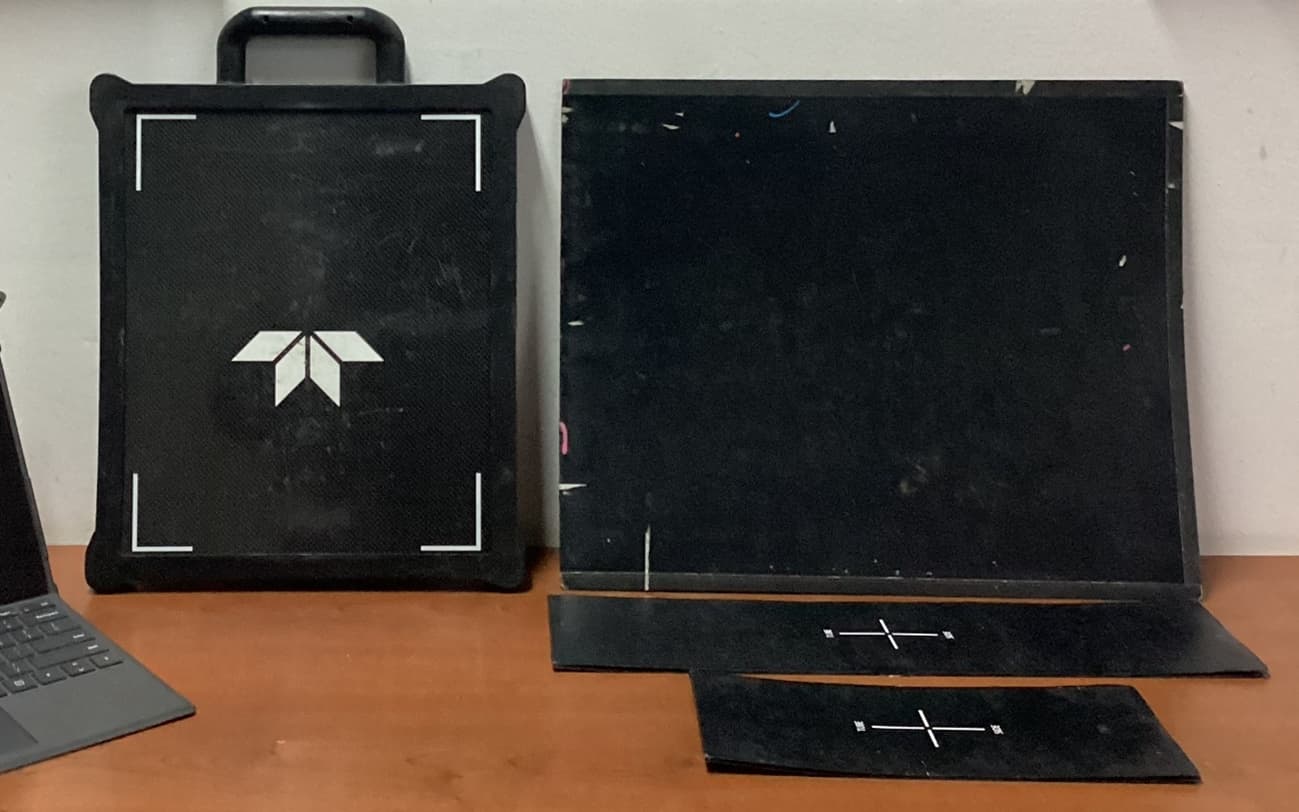
Image 2 Flat Panel and Phosphor Plate
Uses of Digital Radiography
Digital Radiography can potentially be used in almost any inspection where other tests for corrosion detection have traditionally been used. Weld inspection and crack detection were the most common uses, adding with this technology corrosion under insulation, internal corrosion, and defect sizing. These tests can be used in many industries, not just in petrochemical and oil & gas industries.
Seam Inspection: For this inspection, phosphor plates are mostly used. It is often questioned why migrate from the traditional method, as the test can be performed in the traditional way. The great advantage compared to the traditional method is that exposure and development times are significantly reduced. Of course, the advantage of having the digitized plate, a high-resolution image, and being able to measure discontinuities with precision are virtues that help make the decision to migrate to this method.
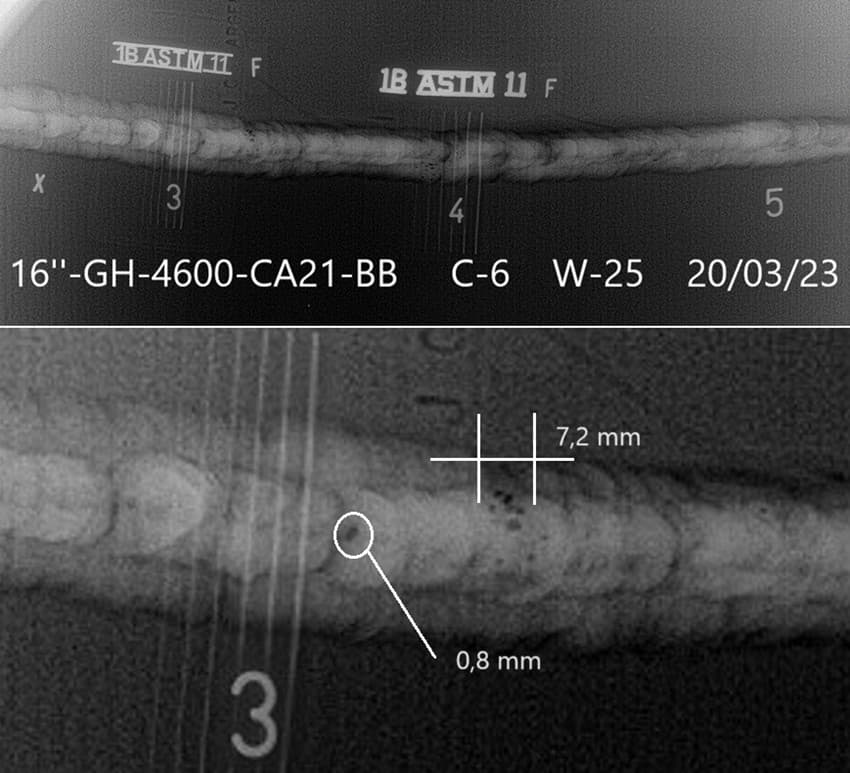
Image 3 Weld inspection record with software measurement of indications
Detection of Corrosion Under Insulation: For the detection of Corrosion Under Insulation (CUI) without needing to remove it, other non-destructive testing methods such as Guided Waves or Pulsed Eddy Currents (PEC) are recommended. Of course, these methods are a screening, and once a CUI area is detected, it is a recommended practice to perform digital radiography using a Flat Panel or, failing that, a panoramic phosphor plate. This will provide the dimensions of the defect.
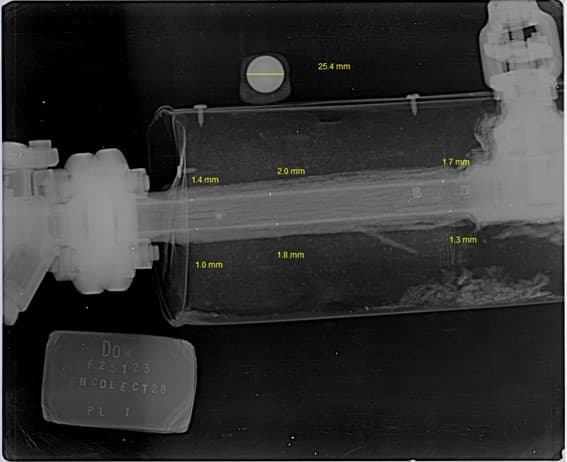
Image 4 Corrosion under insulation inspection record
Detection of Internal Corrosion: This type of inspection is generally performed by conventional ultrasound or Phased Array. There are several and great advantages to using Digital Radiography: covering 100% of the area to be inspected; it has no limitations with small diameters or piece geometries; acquiring the full dimensions of the defect, not just the depth with a smaller margin of error than conventional ultrasound.
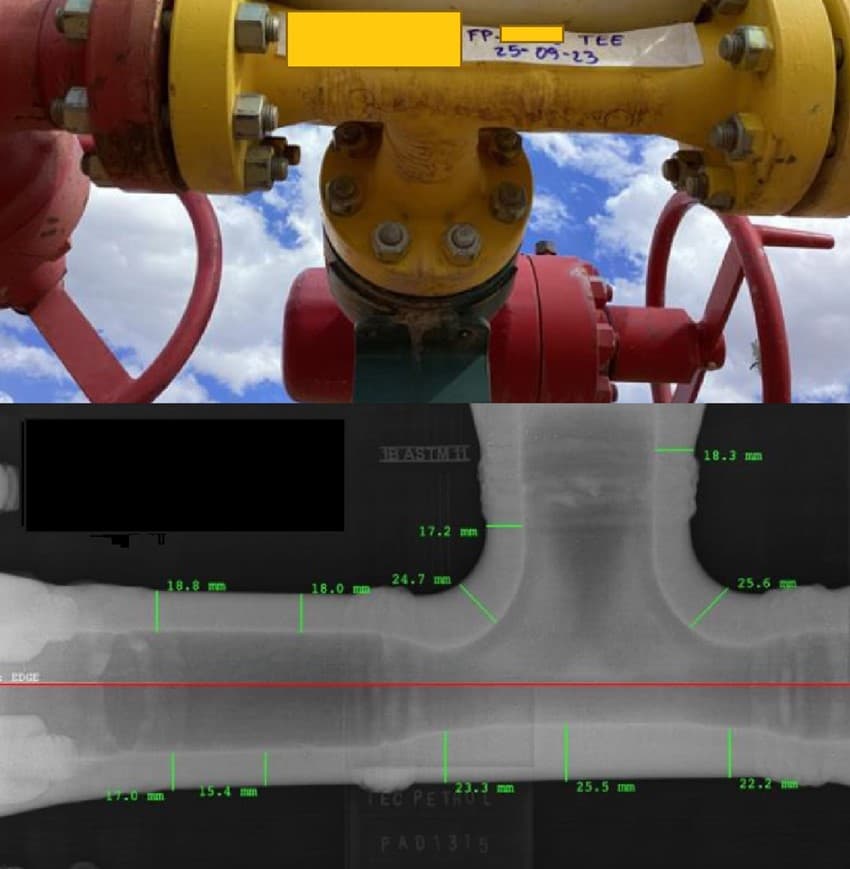
Image 5 Dimensional control and corrosion search in Tee accessory
Verification of Valve Condition: Sometimes check valves are damaged and do not fulfill their function. The plate may be stuck, corroded, the pin may be loose or broken, or the plate may no longer be there. Additionally, in the case of valves located at wellheads where sand is produced, the combination of this abrasive material with the valve geometry can cause erosion, even perforating part of the valve. It is crucial to identify and address these possible damages in a timely manner to ensure the correct functioning and safety of the systems in which these valves are used. The way to verify this is by disassembling the valve and performing a visual inspection, but with digital radiography, using a flat panel, it can be perfectly observed and evaluated.

Image 6 Check valve condition inspection
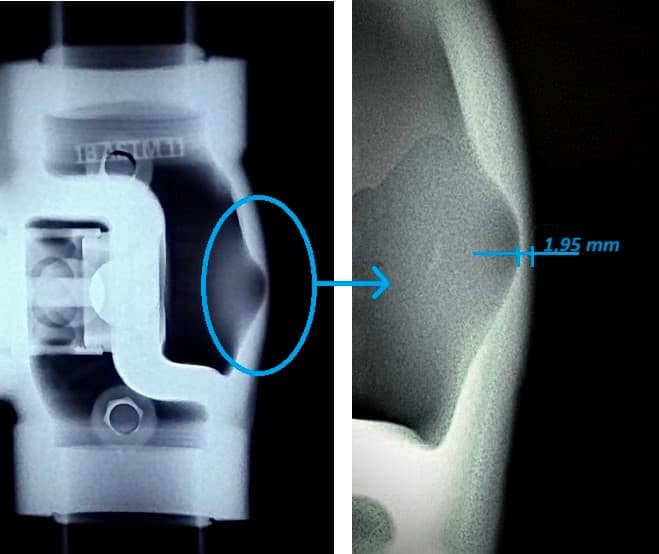
Image 7: Erosion wear detected using Flat Panel and the remaining wall of the valve was measured
In conclusion, the adoption of digital radiography in the oil & gas industry and generally in all industries has not only revolutionized the way structural integrity inspections and defect detection are conducted but also extended its applications to new areas. The significant advantages in terms of reducing radiation exposure time, improving image quality, ease of storage and analysis, and the elimination of chemicals, among others, make digital radiography an essential and increasingly indispensable tool in modern industry. This technological evolution not only optimizes inspection processes but also contributes to safety and environmental sustainability, positioning digital radiography as the future of non-destructive evaluations.