While pipes are manufactured to be used underground, the truth is that a large percentage of them often remains in storage for extended periods of time. The design does not account for prolonged atmospheric exposure. This storage is often spontaneous, without scheduling, and, worse yet, without a maintenance plan or subsequent fitness for service evaluation.
In the case of three-layer extruded coating (PET), despite all the factory’s PQT/PPT (Procedure Qualification Test/Pre-Production Test) controls, there has been a severe worldwide issue characterized by poor adhesion for several years. The severity lies in the screening of cathodic protection that such coatings produce, allowing the advancement of corrosive processes that are difficult to detect using electrical means.
Before polyethylene faces service conditions, it undergoes some damage during the coating process in coating plants, where it is exposed to high temperatures for varying periods and subjected to numerous cutting efforts, depending on the process conditions and its viscoelastic properties. It is also likely to undergo new structural changes due to melt crystallization, orientation during the process, and deformation-induced stress. All of this affects the composition, structure, and morphology of virgin polyethylene and can result in less durable material or an improved product, depending on the process conditions. Such a wide range of potential outcomes underscores the importance of the “material history” that contributes to its performance.
What was mentioned above will be aggravated by the use of pipes that have been stored for extended periods under uncontrolled conditions, without proper maintenance, and with a regulatory gap regarding the tests that should be performed before they are put into service. The same requirements used in the factory are often used. While this is a practice that aims to be conservative, the truth is that not all tests performed in the application plant may be appropriate for evaluating fitness after long storage periods.
The stock of coated pipes is a common measure to address integrity events (ground movement, maintenance, failures, changes in the route).
Storage processes usually do not ensure the integrity of the coating, and when the pipe is used, there are doubts about its fitness for service.
Sampling and Definition of Tests
In cases of large stocks, it is necessary to perform a statistical analysis to select the pipes that need to be inspected. The sample size will depend on various factors such as remaining time before installation, laboratory equipment availability to process samples, the acceptable error percentage on the confidence level adopted for sampling, etc. The selection should be made to include all environmental scenarios of the batch: different humidity levels, solar radiation, supported weights (storage height), etc.
Figure 1: Storage of Pipes
It is known that long storage periods can result in premature aging of polyethylene due to the combined action of oxygen and ultraviolet light, as well as in the loss of adhesion at the ends of the pipes (cutback area).
Initial visual inspections should focus on:
- Type of UV protection and its condition
- Types of supports and spacers for the pipes
- Condition of the ends of the coating
- Appearance of the coating surface (shine, even surface, absence of blistering, etc.)
Among other inspections that are often performed are:
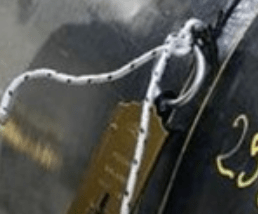
Shore D hardness measurements in the pipe body. Studies of polyethylene degradation processes and academic results suggest that degradation would alter this property.
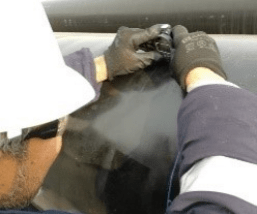
Measurement of coating peel adhesion using a suspended mass technique in both the end and center of the pipe.
Regarding this latter test, it is important to have records both at the ends and in the pipe body. The probability of finding adhesion failures at the ends is often higher due to metal exposure and oxidation, which generates corrosion products in the transition, favoring peeling. In these cases, early detection is important to schedule proper repair during pipe installation and field joint coating. For the laboratory testing phase, a representative coating sample should be taken in advance from all environmental locations and then properly preserved. Since these tests are destructive, it is also crucial to carry out subsequent repairs with material compatible with the coating.
Figure 2: Sampling Process
- Mechanical behavior in tension
- Chemical analysis using Fourier Transform Infrared Spectroscopy (FTIR)
- Melt Flow Index (MFI)
- Oxidation Induction Time (OIT)
Let’s see what each of these tests consists of and what they contribute to the evaluation process:
Mechanical behavior in tension:
This involves applying stress in the same direction as the longitudinal axis of the test specimens. From all the tensile tests conducted, a graph with stress-strain data recorded can be extracted, from which the elastic and plastic behavior of a material can be determined, as well as quantifying, for example, its maximum or rupture strength. Deteriorated polyethylene exhibits greater fragility and loss of elasticity.
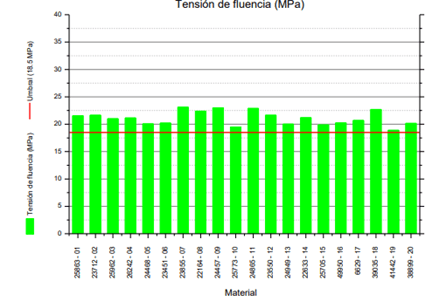
Chart 1: Yield Strength
Rupture strain values often deviate from specifications due to fractures, indentations, and tears that occur during sample extraction.
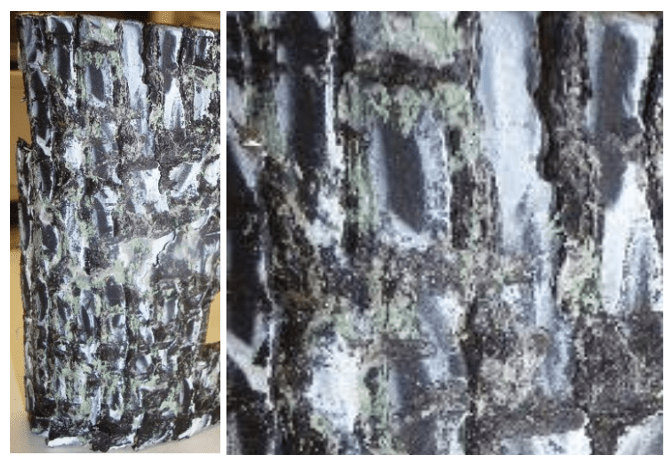
Figure 3: Samples with indentations
Fourier Transform Infrared Spectroscopy (FTIR):
Fourier Transform Infrared Spectroscopy (FTIR) allows for the identification of chemical bonds through the absorption of infrared energy characteristic of the different vibration modes of the bonds. The energy at which these vibration modes are observed depends on the groups present in the bond’s surroundings. This test allows for a basically qualitative and semi-quantitative assessment of the chemical species present.
Through comparison with the original material, the absence of certain species would indicate a degree of deterioration in the polyethylene.
Below are some characteristic signals that can be found in samples of commercial polyethylene:
Wavenumber (cm-1) |
Associated Bonds or Functional Groups |
720 and 1460 |
Signals related to the sample’s crystallinity. |
910 – 990 |
C=C double bonds. Vinyl and vinylidene groups. |
1050 – 1200 |
Additives added to the formulation. |
1180 |
Branches. |
1270 – 1370 |
Gel formation (cross-linking). |
1700 – 1780 |
Carboxylic acids, ketones, and esters. |
2800 – 3000 |
Stretching of the C-H bond. |
Table 1: Fourier Transform Infrared Spectroscopy (FTIR)
The following is an example of the analysis of different samples collected from stored pipes. The spectra of all the samples show signals that do not correspond to the structure of the polyethylene molecule in the 1800-1660 cm-1 and 1200-940 cm-1 regions. These peaks could be related to additives necessary for processing. Differences in the relative intensity of these peaks are observed among the different samples, although they are present in all cases.
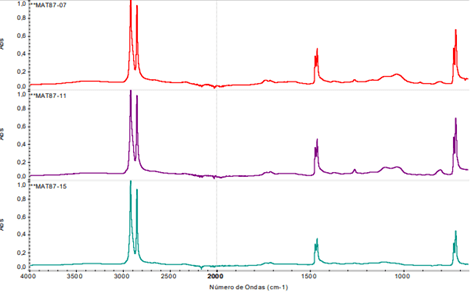
Chart 2: Analysis of Different Samples Collected from Stored Pipes
Melt Flow Index (MFI):
MFI is a measure of the flowability of a thermoplastic polymer when pressed through a 2 mm diameter nozzle. The test is performed at 190 °C with a 5 kg load. The result is expressed in mass (grams) collected in 10 minutes (g/10 min).
MFI is used as an indirect measure of the polymer’s molecular weight, which is valid for highly linear polymers. Its use as a comparative value between materials of different polydispersity or branched polymers is much more complex. In this case, a considerable decrease in MFI could be associated with cross-linking, while an increase could be related to a decrease in molecular weight due to chain scission.
Oxidation Induction Time (OIT) and melting temperature:
OIT values are obtained from an isothermal study at 200 °C, extended for 2 hours, performed in a Differential Scanning Calorimetry (DSC) calorimeter using oxygen as the sweep gas. Differential scanning calorimetry (DSC) provides the heat delivered or extracted from the sample as a function of time. If during the isothermal scan period the sample undergoes changes generated by exothermic or endothermic processes (oxidation degradation in this case), the thermograms exhibit, to compensate for what is generated by oxidation, a peak associated with the extracted heat flow. OIT is determined as the time elapsed from the start of the isothermal scan to the onset of this exothermic peak and depends on the content of antioxidants added as additives in the commercial formulation. OIT variation could be a signal of the loss of these additives and the resulting material degradation. For medium or high-density polyethylene, variations in susceptibility to oxidation may exist related to the presence of processing additives.
Additionally, melting temperature and heat of fusion are determined as they provide information about the crystalline structure of the material. Polyethylene is a semi-crystalline material. Polymeric chains have the ability to organize into local crystalline structures. The regions between crystals are amorphous (structureless). Determining the melting point (TF) and the heat required to melt the crystalline structures (DHF) allows for the characterization of the type of polyethylene.
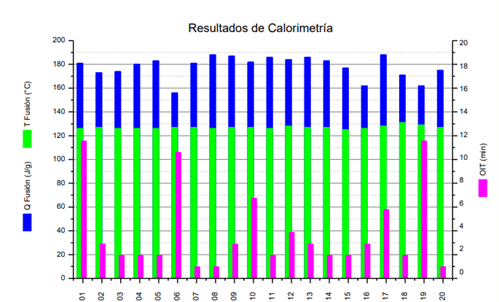
Chart 3: Calorimetry Results
Variability in Oxidation Induction Time (OIT) results is common since variations in susceptibility to oxidation may exist due to the presence of different amounts of processing additives that have remained in the polyethylene after the high-temperature application process. Therefore, this parameter should be analyzed with caution.
Conclusions
A large percentage of pipes remain in storage for long periods, often spontaneously and without proper maintenance programs. It is, therefore, necessary to conduct an aptitude assessment for service by qualified personnel.
Current regulations lack details about the selection of tests to be conducted, so it is common to use the same requirements as those used in the factory. While this practice aims to be conservative, not all tests conducted in the field may be appropriate for evaluating aptitude after long periods in storage. We have shared some tests that are currently being implemented in the Oil & Gas industry to set precedents or best practices in response to this current regulatory gap.
The lack of storage procedures or regulations, along with the absence of Integrity Evaluation procedures prior to the use of these pipes, may lead to undesirable situations in the future:
- The batch of pipes may deteriorate beyond repairable limits, resulting in a significant loss of assets.
- Deteriorated pipes may be dispatched for the construction of pipeline systems, unnecessarily reducing their service life from the outset.
Under these circumstances, it is necessary to deploy a responsible integrity strategy for the conservation and use of pipes in stock, which are essential for infrastructure expansion processes currently underway in Argentina.