Se observa que el cálculo del espesor requerido en todos los códigos, está basado en la fórmula de Barlow, que evalúa la tensión circunferencial en ductos o recipientes cilíndricos, resuelta para el espesor.
El resto de los factores involucrados cubren, por ejemplo, los siguientes aspectos:
- diferencias de resistencia de la soldadura considerada con respecto al metal base, incluida en factores como E o W.
- pérdida de propiedades del material en función de la temperatura,
- riesgo admisible para cada aplicación, que se considera directamente en factores como y o en las tensiones admisibles, en factores como SE, y, o T
- respuesta del material a determinados mecanismos de daño, como los asociados a la presencia de hidrógeno, considerados en factores como C o .
Este método, basado en la ecuación de Barlow, no se puede trasladar al diseño de accesorios que no presentan simetría de revolución, por lo que están sometidos a estados tensionales más complejos. El criterio general para la selección y especificación de los accesorios es que su resistencia a la rotura en un ensayo de presión interna sea al menos igual a la del piping/ducto asociado.
El fabricante es quien debe asegurar y certificar esta capacidad, proceso que por norma puede incluir cálculos analíticos y/o pruebas hidráulicas o modelado FEA.
Todas estas determinaciones estarán basadas en propiedades mecánicas del material utilizado, el que también debe ser química y mecánicamente similar al de la tubería. Las tensiones que se generan en los accesorios son mayores y más complejas que las del tramo recto, por lo que no se asegura la aptitud del accesorio especificando solamente el espesor y las propiedades mecánicas del material iguales a las del tramo recto asociado.
Para cumplir con los requisitos de diseño, suele suceder que algunas partes de los accesorios deban tener mayor espesor que la pared de la tubería asociada [B 16.9, Parágrafo 2.2.2]. En los cálculos de resistencia se deben considerar dichas variaciones de espesor y esto debe quedar debidamente documentado y disponible para que el comprador lo verifique, como así también los registros de pruebas hidráulicas, si fueron usadas como medio para determinar el rating del accesorio.
La prueba de presión
Previo a la entrada en servicio, las instalaciones deben mandatoriamente ser sometidas a una prueba de presión (PP) que se realiza a presiones mayores que la presión de diseño. El exceso por sobre la presión de diseño varía según el código, limitada a no superar generalmente el 90% de la Tensión de Fluencia Mínima Especificada (SMYS, por sus siglas en inglés) de los materiales instalados.
Por su parte los accesorios, que exponen concentradores de tensión altos, pueden sufrir tensiones secundarias mayores a la de fluencia del material. Esto no presupone una falla del elemento ya que las zonas afectadas representan un volumen de material reducido respecto del total y tanto el endurecimiento por deformación y el reacomodamiento de tensiones limitan la posibilidad de rotura en la PP.
Está claro que la plastificación localizada, por escasa que sea, resultará en deformaciones permanentes que no afectan la función y no son evidentes y, a su vez, producen una redistribución tensional que bonifica la estructura para su uso posterior.
Los accesorios se fabrican generalmente a partir de tubos conformados a alta temperatura o soldados, el material sufre grandes deformaciones hasta obtener la configuración deseada. Para lograr las propiedades mecánicas deseadas, se los somete a recalibrado dimensional en frio y posteriores tratamientos térmicos de temple y revenido.
Cuando en el proceso de fabricación no se logran los espesores necesarios, o cuando el tratamiento térmico no genera la resistencia mecánica prevista, aparece el riesgo de rotura en la PP. De hecho recientemente, hemos tenido la oportunidad de ver personalmente, casos donde se ve incrementada la tasa de falla en la PP tanto por estos motivos, como por deficiencias en el proceso de diseño o requisición.
Una falla durante una PP no ofrece riego excesivo dadas las consideraciones de Seguridad que se toman en cuenta durante el mismo. El mayor inconveniente radica en la necesidad de reemplazar los componentes fallados o afectados, realizar nuevas verificaciones y nuevamente la PP. La mayor incertidumbre radica en la confiabilidad de los accesorios que no fallaron.
Este tipo de fallas genera perjuicios económicos, no sólo asociados al reemplazo de los accesorios sino también debido al incumplimiento de plazos por las demoras en la adquisición de los accesorios nuevos. Estos eventos también suelen generan un impacto negativo en la imagen pública de las empresas involucradas.
Causas de fallas recientes en Pruebas de Presión
Analizar la causa raíz de las fallas, en caso de que estas ocurran durante las pruebas, resulta imprescindible para lograr la certificación preoperacional. En ese sentido, en los estudios que hemos realizado en el último año en todos los eventos de fallas asociados a accesorios se verificaron propiedades mecánicas inferiores a las declaradas en los certificados de calidad emitidos por los propios proveedores. También se evidenciaron importantes deficiencias geométricas, principalmente en espesores.
Del mismo modo, en estudios que hemos realizado sobre accesorios instalados que no evidenciaron daños en las pruebas de presión, y en accesorios disponibles en stock de diferentes partidas y proveedores, se encontró que la gran mayoría tampoco cumplían con las propiedades certificadas.
Adicionalmente, se detectó una variación significativa en las propiedades y en los espesores dentro de un mismo componente. Los ensayos fueron complementados con mapeos de dureza, y réplicas metalográficas, evidenciado problemas asociados al tratamiento térmico y al conformado.
Las mediciones de las propiedades mecánicas de los accesorios, tanto instalados como de stock, pudo realizarse mediante técnica de indentación progresiva instrumentada ESYS 10 para PMI (GIE), ver Figura 1. Esta técnica permite obtener las tensiones de fluencia y de rotura de los materiales sin destruirlos, esto permitió identificar los desvíos, generado rechazos por calidad previo a reemplazos y pruebas hidráulicas.

Figura 1: Control de calidad en accesorios adquiridos para el reemplazo, previo a la instalación.
Los resultados de todos los ensayos se compararon con los valores de los ensayos de tracción normalizados, realizados sobre los accesorios fallados. Los resultados mostraron una excelente correlación entre los ensayos de tracción y el ESYS 10 (Figura 2).
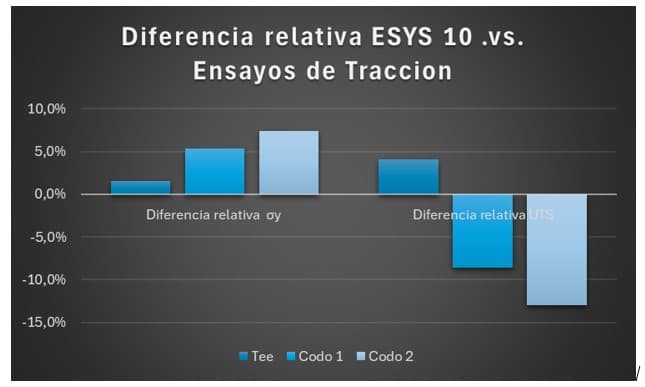
Figura 2: Diferencia entre los resultados del ESYS 10 comparados con los del ensayo de tracción en componentes fallados
Abastecimiento global y retos locales
La posibilidad de que los productos suministrados no cumplan con las requisiciones de compra no es un problema nuevo. Sin embargo, se ha observado un significativo aumento en la frecuencia en la que ocurre este problema en los últimos años.
Históricamente, las empresas trabajaban con proveedores locales o de geografías más cercanas, lo que mantenía acotadas las relaciones comerciales y los proveedores se constituían en actores reconocidos. Hoy en día, el aumento de la competencia global ha permitido bajar los costos, pero llevando a un aumento de los riesgos de no calidad. No es casual que, en todos los casos mencionados anteriormente, los proveedores eran nuevos actores, provenientes de mercados foráneos con poca trayectoria global.
El aumento en el riesgo de recibir un accesorio que no cumple con lo requerido aumenta significativamente y obliga a las empresas a tomar medidas para contener dicho riesgo. Estas medidas pueden involucrar desde una mayor rigurosidad en el control documental, mejores especificaciones de compra, así como ensayos que garanticen la veracidad de los documentos provistos.
Como se evidencia en la Figura 3 (propiedades de accesorios provenientes de 4 proveedores en función de los mínimos requeridos por las normas), la incorporación de ensayos con ESYS 10 para PMI, como hito de control de calidad, permite reducir tiempos y evitar costos de montaje de elementos que no satisfacen los requerimientos de compra, lo cual se ha convertido en un hecho bastante habitual.
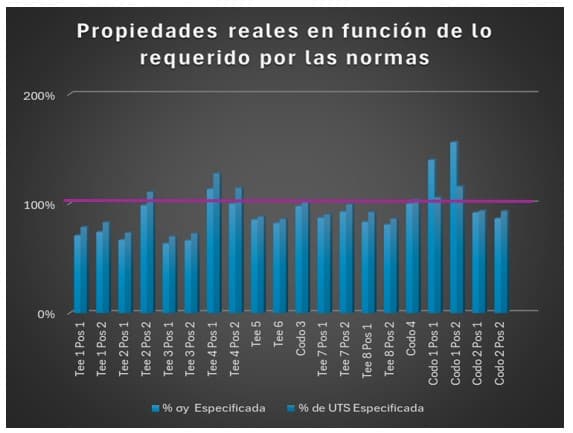
Figura 3: Propiedades reales en función de los requerido por las normas correspondientes. σy: tensión de fluencia. UTS: Tensión última de rotura (Ultimate Tensile Stress)
Conclusiones
Podemos concluir que para evitar los problemas mencionados se debe realizar correctamente las especificaciones de compra, solicitar la documentación de respaldo de los requerimientos normalizados y además realizar ensayos que permitan verificar las propiedades de los accesorios antes de instalarlos. En este último aspecto el ESYS 10 ha demostrado ser una herramienta útil y necesaria para el control de calidad al momento de la adquisición, que permitirá a las empresas ahorrar costos de lucro cesante, reparaciones e impactos negativos en su imagen, mejorando así eficiencia y confiabilidad.