Distintos uso de FEA (Finite element Analysis)
En general (Finite element Analysis) es usado ampliamente en las etapas de diseño y fabricación para tomar decisiones que optimicen la relación costo- beneficio, permitiendo la comparación entre diferentes enfoques y simulando diferentes condiciones operativas y ambientales antes de la creación de prototipos físicos. Esta metodología de abordaje ha significado enormes avances y ahorros de tiempo y dinero.
Del mismo modo, FEA es ampliamente utilizado en los casos de Análisis de falla (FA, failure analysis), Aptitud para el servicio ( FFS , fitness for Service) y Rating, reparación o modificación de sistemas de tuberías, instalaciones y equipamiento y también en la prolongación de vida útil modificando la severidad de las condiciones operativas (Derating)
Utilización de FEA (Finite element Analysis) en el análisis de falla
Cuando se investiga una falla surgen cuestiones a resolver que resultan imperativas. Primero, el más académico y con mejor prensa, es qué se puede hacer para evitar que vuelva a pasar lo mismo. Por supuesto esto está relacionado con disminuir los riesgos, mejorar la operación, evolucionar en el diseño etc. Para esto es necesario determinar cuál fue el modo de falla y cuales lo factores que condujeron a la misma. Otras están más relacionadas con quién va a pagar los platos rotos, valga la redundancia: ¿Cuánto tiempo estuvo gestándose el problema?, ¿El evento resulta inesperado o habría sido detectable?,¿Se hizo todo lo posible, necesario y normativamente obligatorio para prevenir el siniestro?, etc.
En todos los casos el estudio mediante FEA tendrá que contemplar alteraciones de las condiciones originales. Esas alteraciones de las condiciones de diseño provienen de múltiples factores, cambio de las condiciones operativas (incluidos errores de operación), degradación y reducción de espesores por corrosión, alteraciones en sistemas de control, condiciones ambientales, movimientos de suelos, aparición de desgastes, fisuración, daño por fuego, aplastamientos o daño por terceros, etc.
Es muy raro que el AF conduzca directamente a cuestiones de diseño donde todas las variables seguramente ya fueron tenidas en cuenta y validadas en ensayos y experiencias. No se pueden aducir cuestiones de diseño en un motor generador que hace 20 años que está en servicio. Las probabilidades de tener que abordar cuestiones de diseño en el AF aumentan cuando se trata de incorporación de tecnologías en desarrollo.
En todos los casos, el modelado presenta diferentes desafíos debido a que todo lo anterior no produce ni obedece a patrones geométricos fácilmente reproducible en el CAD. Aquí también es necesario definir cuanto se profundiza en los detalles de la defectología en ese compromiso entre obtener resultados confiables y el costo computacional.
El análisis tensional o de cualquier tipo realizado mediante FEA no resuelve por sí mismo todas las cuestiones planteadas, es un elemento de juicio más que completa el panorama que se va formalizando a lo largo del proceso del AF. En términos generales define y separa de mejor manera el campo de lo posible de lo poco probable, y toma relevancia cuando el resto de la evidencia disponible o generada en el AF no señala claramente un único modo de falla. En definitiva, el mayor peso que tiene el FEA es validar o rechazar hipótesis respecto de las causas.
Análisis de Falla mediante FEA (Finite element Analysis) en geometrías complejas
Cuando las partes involucradas en la falla tienen geometrías complicadas que se alejan de los conceptos de tubos, placas o membranas, o cuerpo esbeltos de secciones constantes, el método FEA es (hoy) el más inmediato para identificar los hot points o sitios donde se producen valores de tensiones más elevados. La determinación de estos es necesaria para predecir o justificar la ocurrencia de la iniciación y propagación de fatiga, por ejemplo.
Fatiga y propagación de Fisuras
Para abordar el tema de fatiga hay bagaje teórico y empírico suficiente para llenar bibliotecas, y cantidad de publicaciones a las que es hoy imposible seguirle el ritmo. Hace tiempo que las teorías dejaron de tener nombre propio, y se agolpan anónimamente en las normas que las contienen. Sin embargo, con todo esto y como bien se sabe, el 90 % de las fallas catastróficas se producen por fatiga y siguen ocurriendo
Otro capítulo aparte merece la utilización de FEA en la propagación de fisuras y la determinación de su criticidad. El problema fundamental radica en que la discontinuidad que genera una fisura no es factible de ser abordada mediante el mallado tradicional por la singularidad del extremo de esta, y tanto el crecimiento como criticidad dependen, entre otros, del tamaño de la fisura. El objetivo es determinar el Factor de Intensidad de tensiones de la fisura con suficiente exactitud.
Varios métodos se han ido desarrollado en los últimos años siendo los primeros, el método de las tensiones, de los desplazamientos y el de integral de línea o evaluación de la integral J. También incorporan proceso para predecir el crecimiento, incluso la dirección de propagación. Los métodos para evalúa el crecimiento de fisuras son en general dependientes de malla y requiere el remallado permanente a media que la fisura avanza. Formas de mejorar la precisión y la eficacia del modelado como el eXtended Finite Element Method (XFEM) han sido implementados por los softwares comerciales.
El estudio del avance de mecanismo de daño dependientes del tiempo, como fatiga, corrosión fatiga, o creep, en principio permite la evaluación de la vida remanente del equipo. Hay que tener en cuenta sin embargo que las velocidades de propagación calculadas varían notablemente con las condiciones particulares del medio y de los materiales y de las tensiones residuales. Estas últimas requieren tratamientos específicos dependiendo del mecanismo de generación, como se tratamiento térmico, mecanizado, soldadura, inducida por autofrettage u otro mecanismo de deformación plástica previos
Ejemplos de Aplicación
A continuación, presentamos 3 casos que ilustran la variedad de situaciones donde la asistencia de FEM resulta indispensable para la conclusión del AF
Marine Fender
El modelado de un Panel de defensa de mulle (Marine fender) destinado a la descarga de petróleo de buques, permite determinar el estado tensional al que está sometido bajo las condiciones operativas más severas. Es imprescindible profundizar en la inclusión de los detalles de los internos lo que aumenta el ¨tamaño¨ del modelo. Para poner en evidencia la criticidad de pérdida volumétricas de material debido a efectos de la corrosión de diferentes magnitudes es necesario modificar el CAD para representar debida el daño. Esto permite evaluar la situación y tomar medias a mediano o largo plazo con conocimiento de la severidad de daños.
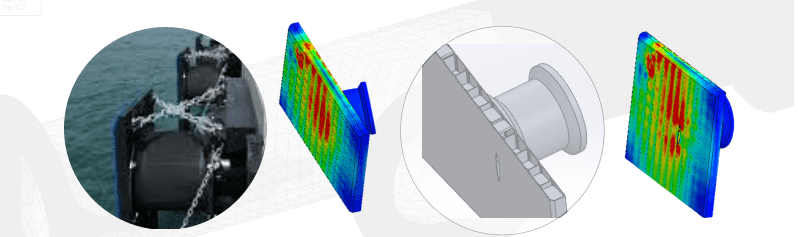
Panel de defensa de mulle (Marine fender)
Soplador
El Análisis de Falla de la rotura catastrófica de un rotor de soplador de gran potencia permite delimitar la causa a problemas constructivo y operacionales. Como verificación de la validez de las zonas o bandas prohibidas de funcionamiento se realizó un modelado CAD 3D del rotor. Este incluye el eje con condiciones de contorno que contemplan los apoyos en los rodamientos con libre alineación angular. Se efectuó un análisis modal y del tensional debido a la aceleración centrípeta y los diferenciales de presión a velocidad nominal.
Los primeros modos normales calculados resultaron coincidente con picos de la medición de vibraciones en el rotor reparado. El estado tensional resultó de niveles aceptables con pico en la zona de iniciación de la fractura. El análisis permite predecir la sensibilidad de esto parámetros frete a la variación de espesores en un rediseño para la reconstrucción de la parte y muestra los puntos son los más críticos frente a la resistencia a la fatiga, y será donde deba centralizarse mayormente la inspección de la calidad de soldaduras.
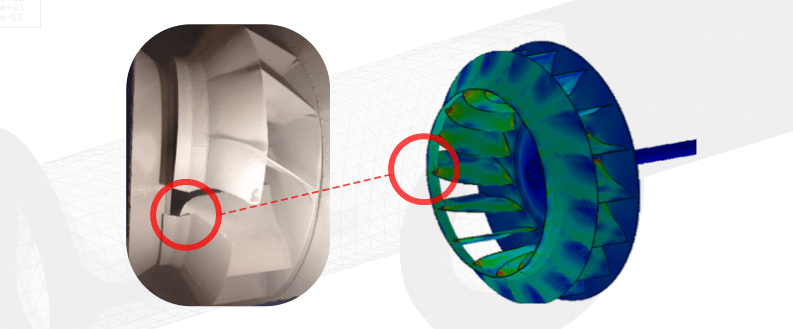
Soplador
Vastago de Bombeo
La falla recurrente de vástagos de bombeo mecánico de equipos AIB tipo Rotaflex condujo a una serie de análisis experimentales, modelos FEA y la generación del árbol de causa – efecto para la determinación de las causas raíz. El modo de falla fue identificado como fatiga con componente tensional de tracción -flexión producida en un lugar por debajo de la cruceta de la eslinga.
Se realizó una inspección en campo orientada a determinar posibles factores que colaboraran en la ocurrencia de las fallas. Se detecto excentricidad de litro de la eslinga respecto del eje de la barra y deformación plástica encontrada sobre los vástagos en la zona de la grampa.
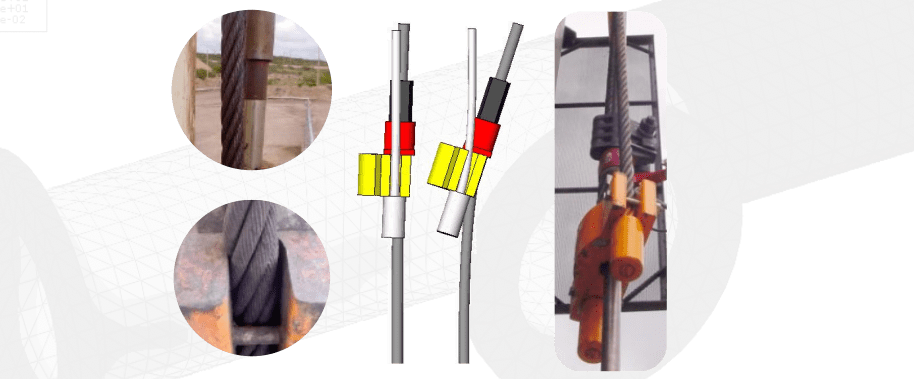
Estado de deformación obtenido del modelo 1x y 5x, A la derecha, se compara con la imagen de la barra con igual excentricidad
El modelado FEA o reproduce el estado de desplazamiento encontrados en campo, en especial el corrimiento de la barra en el extremo superior. El análisis muestra que el estado tensional supera los de fluencia en la zona de tracción. Llamativamente se observa que aparecen también esfuerzos de compresión debido a que la excentricidad de la carga es mayor que le radio del núcleo central de R/4. Se puede hacer un análisis de sensibilidad de las tensiones con la excentricidad.
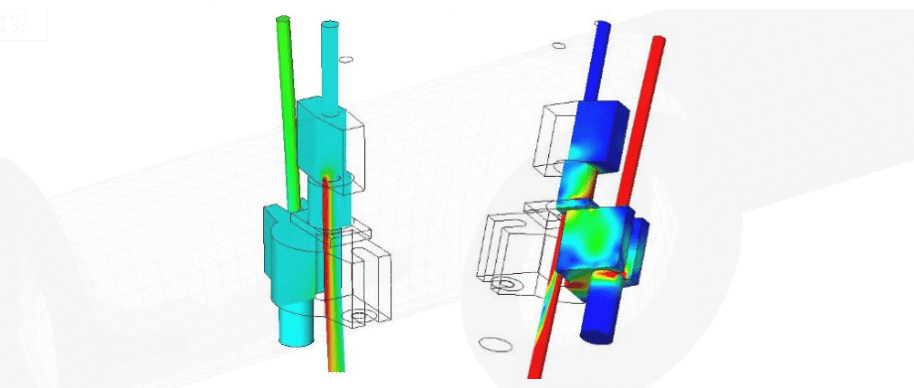
Descripción del estado tensional debido a la excentricidad del tiro de la barra
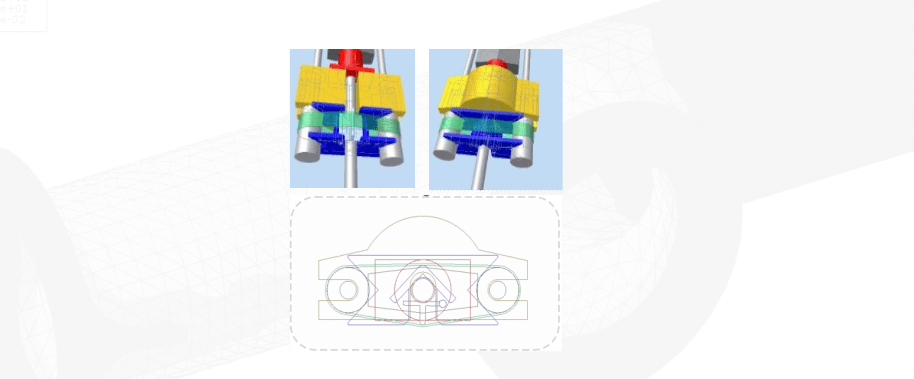
El análisis FEA de los componentes pone en evidencia la criticidad de la excentricidad en el cuelgue de la barra, lo que lleva a proponer un dispositivo centrador para eliminar el problema
Sobre el autor
Anibal Marquez
Ingeniero Mecánico egresado de la Universidad Nacional de Mar del Plata, Facultad de Ingeniería. Cuenta con 23 años de experiencia como Gerente de Proyectos en GIE GROUP.
Perfil Linkedin